Mainline Sectional Repair
- Home
- /Mainline Sectional Repair
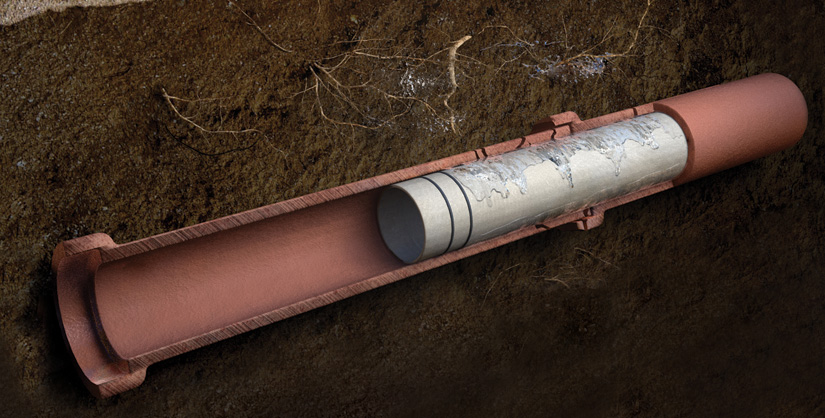
Key Features:
Mainline: Animated Inversion Process
ASTM F2599
Standard Practice for The Sectional Repair of Damaged Pipe By Means of An Inverted Cured-In-Place Liner
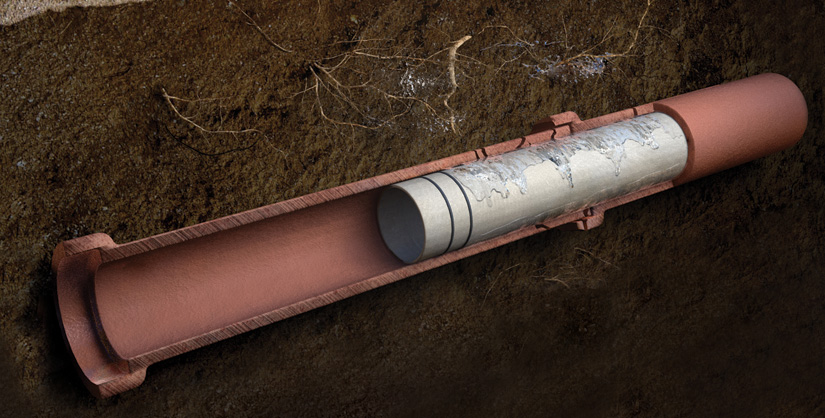
Significance and Use
Purchase the full version of this standard by visiting the ASTM website here. This practice is for use by designers and specifiers, regulatory agencies, owners, and inspection organizations who are involved in the rehabilitation of sewer service laterals and its connection to the main through the use of a resin-impregnated tube installed within an existing sewer lateral. As for any practice, modifications may be required for specific job conditions.
1. Scope
- This practice covers requirements and test methods for the sectional cured in place lining (SCIPL) repair of a pipe line (4 in, through 60 in. ) by the installation of a continuous resin-impregnated-textile tube into an existing pipe by means of air or water inversion and inflation. The tube is pressed against the host pipe by air or water pressure and held in place until the thermo set resins have cured. When cured, the sectional liner shall extend over a predetermined length of the host pipe as a continuous, one piece, tight fitting, corrosion resistant and verifiable non-leaking cured in place pipe.
- The values stated in inch-pound units are to be regarded as the standard. The values given in parentheses are mathematical conversions to SI units that provided for information only and are not considered standard.
- There is no similar or equivalent ISO Standard. This standard does not purport to address all of the safety concerns, if any, associated with its use. It is the responsibility of the user of this standard to establish appropriate safety and health practices and determine the applicability of regulatory limitations prior to use. Particular attention is drawn to those safety regulations and requirements involving entering into and working in confined spaces.
2. Referenced Documents
- D1600 Terminology for Abbreviated Terms Relating to Plastics
- D3681 Test Method for Chemical Resistance of Fiberglass (Glass-Fiber-Reinforced Thermosetting-Resin) Pipe in a Deflected Condition
- D5813 Specification for Cured-In-Place Thermosetting Resin Sewer Piping Systems
- D790 Test Methods for Flexural Properties of Unreinforced and Reinforced Plastics and Electrical Insulating Materials
- F1216 Practice for Rehabilitation of Existing Pipelines and Conduits by the Inversion and Curing of a Resin-Impregnated Tube
- F412 Terminology Relating to Plastic Piping Systems
NASSCO Guidelines
- RecommendedSpecifications for Sewer Collection System Rehabilitation.
Index Terms
Sectional cured in place lining; tube; sheet; vacuum impregnate; continuous; bladder; textile; felt; knit; resin; inversion; inflation; ambient cure; steam cure; launcher; liner/bladder assembly; ICS Number Code 23.040.99 (Other pipeline components)
DOI
10.1520/F2599-16
For a copy of the ASTM F2599-16 Standard please visit www.astm.org.
Mainline Sectional Inversion Submittal
– 30 day chemical resistance LMK Test Results 052308
– DMA TDS
– Flex Report_Item III_Task Ord#3_4-28-100001
– Installation Specification for CIP Sectional Lining
– LMK 656 CIPP Resin Spectrograph
– Microbac Testing D543 Chemical Regeants
– Proper Care of LMK 656 Thermoset Resin
– Tensile Strength Graph_Task Order 6-1_Rec_d 01-07-11_Test_d 01-11-11
– Tensile Strength Test Results_Task Order #6-1_Recved 01-07-11_Tested 01-11-11
Case Studies and Articles
Insignia Gasket Sealing Technology
The Myth, the Fact and the Legend: Insignia Hydrophilic Sealing System
Sahar Hasan, Applications Engineer and Kristina Kiest, Director of Marketing
Published in Trenchless International Magazine, October 2012
Gasket Sealing Technology: A Solution to Sealing Deficiencies in Cured in-Place Pipe Lining
Kristina Kiest and John Vose
Presented at NASTT No-Dig March 2012
T-Liner Main-To-Lateral Connection And Vac-A-Tee Cleanout
A Comprehensive Understanding of ASTM F3097-15 “Standard Practice for Installation of an Outside Sewer Service Cleanout through a Minimally Invasive Small Bore Vacuum Excavation”
Rick Gage and Amana Arayan
Presented at NASTT No-Dig March 2016
Sealing the Connection for Large Diameter Pipes, Trenchlessly
Mike Czipar and Amana Arayan
Presented at NASTT No-Dig March 2016
Rehabilitation of the Coral Gables Wastewater Collection System
Sahar Hasan, Mark Gulyas, and Jorge Acevedo
Presented at NASTT No-Dig April 2014
A Technique for Renewing a Section of Mainline Pipe while Simultaneously Renewing Multiple Service Lateral Pipes through the Use of Continuous CIPP
Larry Keist and Sahar Hasan
Presented at NASTT No-Dig 2012
Lining Laterals in Las Olas
Kristina Kiest
Published in Trenchless Technology Magazine, October 2010
A Comprehensive Understanding of ASTM F2561-06 “The Standard Practice for Rehabilitation of a Sewer Service Lateral and its Connection to the Main Using a One-Piece Main and Lateral Cured-in-Place Liner.”
Larry Kiest, Jr. and Rick Gage
Presented at NASTT No-Dig March/April 2009
Trenchless Technologies; Quicker, Cleaner, Greener and Cheaper Ways to Get the Job Done
Kristina Breese
Published in the Professional Engineer, Spring 2008
Multiple Technologies – Maximum Flow Reduction
Northcrest-Afton Sewer Rehabilitation Project, New Castle County, Delaware
James W. Shelton and Michael T. Harmer
Presented at Mediterranean No-Dig, September 2007
The Lateral Lining Market Has Arrived: Lateral Work is Being Completed in All Corners of the World with More on the Way
Joan Blythe
Published in Trenchless Technology Magazine, April 2007
Trenchless Rehab from the Engineer’s Perspective
James W. Shelton
Published in Trenchless Technology Magazine, October 2006
Prince William County Service Authority Project Case Study
Shaun Flannery and Larry Kiest, Jr.
Published 2005
Wisconsin Raises the Bar Utilizing T-Liner
Shaun Flannery
Published 2003
Fighting the Tide; Installing and Rehabilitating Sewers Using Trenchless Techniques; Boston Water & Sewer Commission
Irene McSweeney Woodfall, P.E. and Michael Oliveira
Conference Proceedings, NASST No-Dig 2000
A Case Study In Infiltration Reduction through Trenchless Technology
South Palos Township Sanitary District, Cook County, Illinois
Aaron E Fundich, P.E. and Larry W. Kiest, Jr.
Published March 1999
Lateral Lining
Local Ordinances Dictate Lateral Renewal Technologies
Larry Kiest and Rick Gage
Presented at NASTT No-Dig 2010
Portland BES Advances in Sewer Maintenance and Repairs by Operating Multiple CIPP Crews
Joe Dvorak and Larry Kiest, Jr.
Presented at NASTT No-Dig April 2007
Criteria for an Effective Lateral Renewal Project Utilizing Trenchless Technology
Larry Kiest
Presented at American Society of Civil Engineers (ASCE), New Pipeline Technologies, 2003
Lateral Thinking
Keith Gribbins
Published in Trenchless Technology Magazine, April 2002
Sectional Spot Repair
Steam Cured Large Diameter CIPP Sectional Liners Make Fast Repairs in Sensitive Environmental Areas
Joan Blythe
Published October 2012
Siphon Spot Repairs in Tampa
Larry Kiest, Jr.
Published October 2010
CIPP Sectional/Point Repairs; Critical Factors – Finally Explained
Shaun Flanery
Published May 2010
Lined Main Tap
Every Lateral in Dane County gets a new Connection Using the LMK Lined Main Tap
Kristina Kiest and Larry Kiest
Published February 2011
Manhole
The Most Cost Effective Method for Eliminating Inflow
Larry Kiest
Presented at American Society of Civil Engineers (ASCE), Pipelines, 2006
Research
The Inspector is the Gatekeeper to a Successful CIPP Installation
Larry Kiest, Gerry Muenchmeyer, and Amana Arayan
Presented at NASTT No-Dig 2015
Protocols for the Quantification of Water-Tightness of a Rehabilitated Main/Lateral Sewer Connection
Rick Gage
Presented at NASTT No-Dig March 2011
Making it Stick; Contractors repairing sewer laterals with CIPP linings need to consider multiple factors that affect the quality of the lateral-to-main connection
Larry Kiest, Jr.
Published at the Pumper & Cleaner Environmental Expo International, February 2006
Verifiable Non-Leaking Connection Where No Water Migrates
Larry Kiest and Shaun Flanery
Presented at NASTT No-Dig 2005
Testing Top Hat Liners and Robotic Systems for Repair of Lateral Connections
Dr. -Ing. Bert Bosseler and Dipl.-ing. Gunther Kaltenhauser
IKT – Institute for Underground Infrastructure, Published June 2004